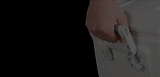
CASE STUDY
Two-Shot Molds Help Produce Softer-Feeling Handle
From conception to completion, every plastic injection mold A1 builds is recognized for world-class quality. This comes down to our process and how we work with our customers and within our own teams to exceed expectations. We strive to get it right the first time.
Our attention to detail, thorough review and communication with our customers is what helps us achieve success. It’s this mix of teamwork and strategic alliances with our customers, employees and community that enable us to provide innovative quality solutions
| Partnership with A1
Why Coleman partnered with A1: The customer had previously purchased a mold that they wanted replicated to fit this particular project. They were so pleased with the original, they wanted to expand the relationship with A1 to include their mold in this project.
Expectations of Partnership: While the first mold was also created for the handle of a cooler, this new mold would be used on high-end, larger coolers. The handle would be created to be softer, helping with the grip on larger coolers that fit more and are subsequently heavier.
Benefits A1 Offered: A1 was able to produce the mold Coleman wanted with the softer look and touch, which would make the product appealing to customers.
Company Overview
-
Industry: Manufacturing
-
Company goals: To provide the most reliable, innovative outdoor camping gear.
-
Company vision: To be an innovator in creating experiences that can’t be found inside.

| Pain Points / The Challenge
When Coleman approached A1 about the project, they already had the part in mind. The first product they worked on with an A1 mold was plastic handles for a cooler. This time, they knew they wanted a softer handle that would be more visually and physically appealing to the consumer. The first project had gone so well that A1 was their first choice for the new product.

A Superior Product
“We are pleased to be working with A1 Tool Corporation on yet another project. We love their mold because it produces good parts at cycle that are appealing to our customers.”
Zachary Thompson, Senior Manufacturing Engineer – Wichita
The Coleman Company — Outdoor & Recreation Division
Newell Brands
| Future vision
Since first working together in 2016, the relationship has remained steady and productive. After producing an initial mold for Coleman’s cooler handles, they’ve again included us in this new handle design project. We’re replicating our original work, while refining the look and feel. Looking to the future, we’ve got the potential for more projects together. We see a productive long-term relationship between Coleman and A1 Tool Corp over the next several years.
Learn how A1 Tool Corporation can provide solutions to your business →
