INJECTION MOLD AND TOOLING
Specialty Tool Design and Engineering
From pencils and drafting tables to CAD (Computer-Aided Design) and Moldflow Analysis, A1 has drastically changed from its 1946 roots. From those initial roots and through thousands of designs and highly trained, educated, and skilled designers come some of the most innovative engineering solutions. Our team of on-staff designers love a good challenge, where they can collectively find an economical and repeatable solution for your needs.
Consolidating multiple parts into a single mold, complex geometry, multi-action, multi-shot, or family stack molds, no challenge is too great.
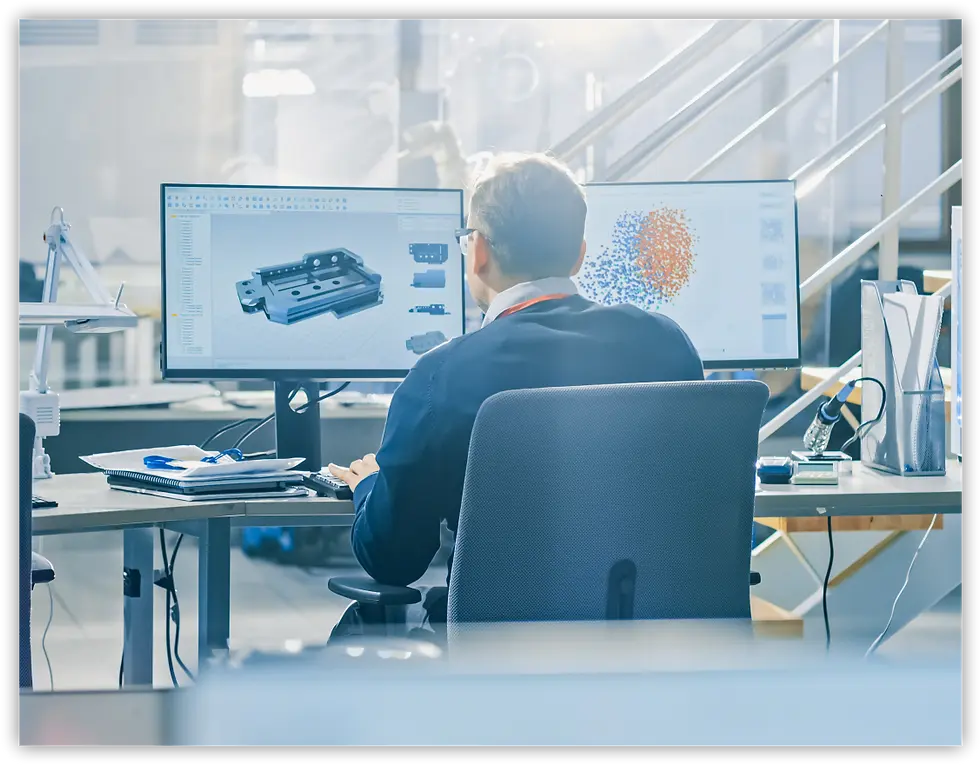
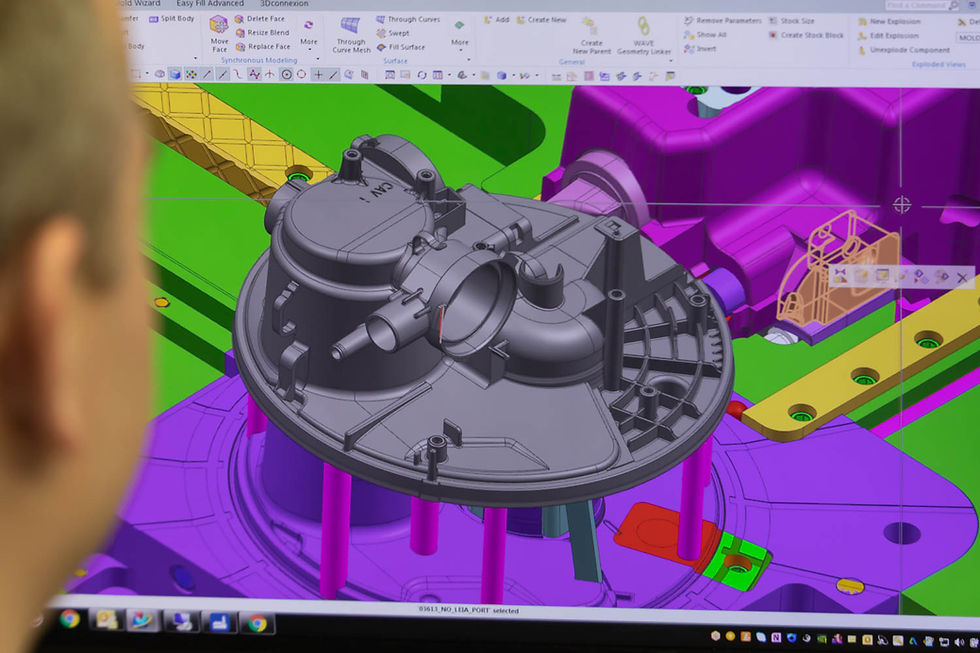
Computer-Aided Design
Our engineering experts will collaborate with you to create dynamic solutions with the most robust design and functionality. We are creative thinkers who build tools to the highest standards with state-of-the-industry equipment. Our in-house design, manufacturing and mold sampling ensures accurate parts with the productivity and innovation you need.
WHAT CLIENTS SAY

"They are by far one of the top engineering departments / believe for injection molders. Very thorough, very precise, understanding all the dynamics of the part design and how to mirror that over to a mold design.
That's what first and foremost sold me."
TIM RUYBAL, SENIOR ACCOUNT
ENGINEERING MANAGER, INTERTECH PLASTICS
WHAT CLIENTS SAY

"They're knowledgeable. I can't stress that enough. I mean, they'll see something in the design of the part and say, "Listen. That's not going to work. Can we do it this way?" And they'll work with the design engineers to change it to the right way."
JOE VEZZOSI, TOOLING MANAGER, ELECTROLUX
WHAT CLIENTS SAY

chris Kuczek
WHAT CLIENTS SAY

Melodyy Yy
WHAT CLIENTS SAY

Darek P
WHAT CLIENTS SAY

Adam Molski
WHAT CLIENTS SAY

KiwiKing
WHAT CLIENTS SAY

Kimberly Ray
WHAT CLIENTS SAY

Receiving
Vasyl Tkach
WHAT CLIENTS SAY

Always nice people in shipping and receiving!!!
They receive till midnight. Some parking on the side of the street.
D H
WHAT CLIENTS SAY

We had fast and friendly service on our transmission jack which made A1's services worth the extra $$$! This was unexpected considering we are almost 2.5 hours away. Thanks guys.
Cameron Hart
